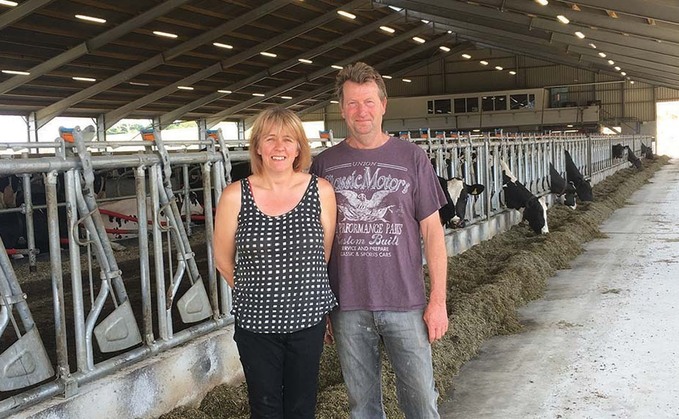
Switching milking systems has gained traction over the past decade, with farmers wanting to upgrade technology and reduce milking labour. For one farm a dual approach is creating flexibility for the future. Natalie Noble reports.
Swapping out one milking system for another is no small feat. The long-term impact on productivity of both herd and workforce generally makes it a worthwhile investment - but there is always still some risk attached.
So when dairy farmers Chuck and Michele Baulch chose to invest more than £1 million in modernising their dairy farm, they paid particular attention to potential risks and limitations.
Having helped to grow the Baulch family's dairy business from a small British Friesian herd to 250 Holsteins, Mr Baulch and his wife took on Great Cocktree Farm, North Tawton, Devon, in the late 1990s. Now, they have taken another big step, installing a housed robotic system with their conventional 20:20 herringbone parlour still in operation.
Mr Baulch says: "The progression of the farm has always been a focus. Whatever we do we are always thinking about the future - what will secure the business not only for us but for our children as well."
He adds they would like to increase cow numbers from 265 to 350 but were limited by capacity provided by the conventional milking parlour.
"We needed to modernise, which involved looking at the milking system, housing and slurry handling."
Robotics
In spring 2018, after consultations with advisers and visiting a variety of farms with different systems and cow husbandry, the Baulchs decided on a housed robotic system. Mr Baulch says: "The high yielding pedigree Holstein seemed to really do well in the controlled environment, and we could design and use space to improve slurry handling and labour efficiency."
In January 2019 groundwork started on the greenfield site after 12 months battling for planning permission.
Mrs Baulch says: "The council had concerns over flood risk and water runoff from the roof structure - they became expensive sticking points, but we were granted permission eventually."
However, a full transition to a housed robotic system was not practical, and the couple knew they would have to keep and update the conventional system to overcome challenges.
Mrs Baluch adds: "We could not justify building for 350 cows we did not have, but we could not afford to reduce our numbers to fit one system. Staff retention was also important and downsizing would have made that difficult."
So to maximise efficiencies and retain the option to expand over time, they decided to incorporate both systems and connect to the same milk silo.
Splitting the herd into high and low yielders, the couple moved 140 of their highest yielders to the housed robotic system on January 28, 2020, while the low yielders - typically less than 24 litres or with health issues - were kept in the conventional rotated grazing system.
Mrs Baulch says: "The two groups make for better management and our labour is no longer centred around milking. Both high and low yielders are now working in systems that meet their needs and level of production, which has only improved things as a whole."
In the four months since their move into the housed robotic system, the 140 cows are producing on average 40 litres per day - about six litres more than before the switch - with milk solids of 3.2 per cent protein and 3.9 per cent butterfat.
Calving all-year-round, the cows are moved into the robotic system seven to 10 days after calving, with two weeks of robot training if necessary. They stay in this system until they are eight weeks pre-drying off, at which point they are moved to the conventional system.
Information
Technology is truly a driver in the Baulch's robotic set up. Mr Baulch says: "The cows wear collars which communicate with the robot. We can monitor individual yields and milking speed per quarter, conductivity of milk, cell counts, bodyweight, temperature, rumination, how much they are eating and their activity.
"This information lets us know if something is not quite right, like poor health, a long time before it becomes a problem. Alongside an improved environment it has reduced antibiotic usage by 80 per cent."
The couple thought out the unit's environment carefully with their Lely consultant and Ivor Davies at CowPlan.
Mrs Baulch says: "Getting the environment right matters, so we invested heavily in cubicles, manure management and lighting."
The cubicles in the housed unit are designed for correct body placement and to keep beds and cows clean, with the cows visibly lying for longer but times yet to be recorded. The roof has a central ridge overlap and sides have windowed bays, promoting air circulation and better temperature consistency.
To maintain cleanliness and foot health the Baulchs invested in an automated manure scraper which pushes manure from the passages through the slatted floor and into the under-floor slurry cellar. This cellar has increased storage capacity from 15 months to 18 months and reduced the farm's environmental impact with no requirement to build a new lagoon on a separate site.
With high levels of production, the couple wanted to make sure feed was always in front of the cows, so they invested in an automated feed pusher which discourages sorting and improves intakes.
With the potential to increase milk yield by 6-10 per cent through optimum lighting, they installed an LED lighting system which provides 200 lux of light for 16 hours a day, with the remaining eight hours at 80 lux - a replication of a summer's day and moonlight.
Conventional system
Low yielders are rotationally grazed and milked in the conventional parlour. The manual labour required gives the herdsman more control of individual cow treatment at drying off or through illness. And by splitting the groups the Baulchs have seen far better utilisation of forage and feed.
Mr Baulch says: "Under the conventional system we did not have the ability to feed different rates - everything was feed to the same literage which was obviously impacting feed costs per litre produced. That is no longer an issue for us; with the low yielders separated, we buffer feed to the 24-litre average they are producing and have set up a weekly rotational grazing platform while we save the better forage for cutting and ensiling for the high yielders."
The money spent on updating the herringbone parlour brings the two systems together, giving the farm flexibility in management of all their cows, adds Mrs Baulch.
"Efficiencies have definitely improved as well as sustainability; average yields have increased and we are on our way to producing 12,000 litres per lactation," she says. "Improved health and welfare address the wants of our Arla contract and also of the end consumer, who are wanting food produced to high standards."
Housed robotic system
- Agricultural building (37m by 72m)
- 180 cubicles with mattresses
- 180 locking yokes
- Three robotic milkers
- Nine fast draining water troughs
- Integrated gating system for grouping
- Clean room with operator access to robots
- Chemical store
- Gallery office
- Feed passages down both sides (5m by 72m)
- Slurry cellar (64m by 25.6m by 3m = 3,440m?)
- Manure scraper and automatic feed pusher
Build Figures
- £1 million groundwork to completion
- £200,000+ building
- £140,000 slatted concrete floor
- £400,000 robots
- £50,000 cubicles and mattresses
- £50,000 slurry sellar
- Plus groundwork, planning, labour and parlour update costs
51AVÊÓÆµfacts
- 175 hectares (432 acres) owned and rented
- 265 milking cows plus 250 followers and 100 beef animals
- Herd three-quarters pedigree Holstein
- 9,000 litres per lactation before robots
- 10,500 litres per lactation budgeted
- 12,000 litres per lactation target
- 40 litres robotic average yield
- 24 litres average low yield
- 3.2 per cent protein
- 3.9 per cent butterfat
- 1,500 litres from forage
- Arla liquid contract
- Build start January 2019 and completed January 2020
- 15 per cent ROI