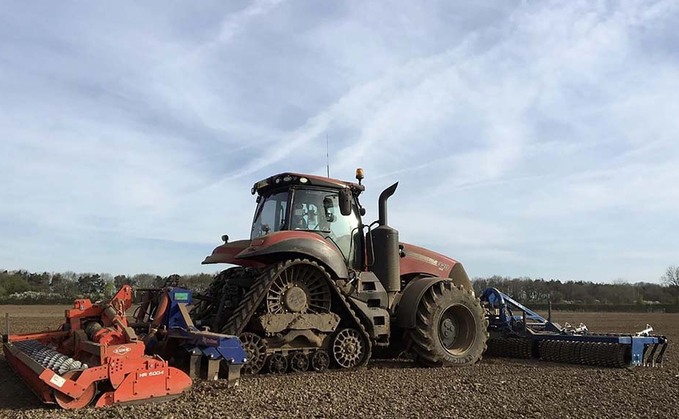
Like getting your money’s worth? A Warwickshire farming business is deploying high power tracklayers for a wide range of jobs, reports Jane Carley. Brinklow Biogas is a diversified farming business...
Like getting your money’s worth? A Warwickshire farming business is deploying high power tracklayers for a wide range of jobs, reports Jane Carley. Brinklow Biogas is a diversified farming business...
2014 Used Massey 7626 7.4L SISU 240hp
Used Deutz Fahr 6155PS
New Kubota M4-073